0 前言: 河南省安阳化学工业集团公司造气一车间常压脱硫,承担着老区合成氨、甲醇、甲胺三系统的脱硫任务,设备装置是原设计“六改八”92年上的一套脱硫设备,现已扩大到年产12万吨合成氨;九五年又新上一套年产三万吨甲醇项目,现已扩大到六万吨以上,半、水煤气量达96000Nm3/h 。三系统脱硫液共同循环使用。 1 脱硫主要设备规格 脱硫塔两台: 合成氨系统:Ф4400mm H 38850mm 甲醇系统:Ф2800mm H 38850mm 塔内装:100×100mm鲍尔环填料 喷射再生槽三台: 合成氨系统两台:Φ4800/Φ5700mm H6600mm Φ3500/Φ4400mm H 6600mm 甲醇系统:Ф4500/Ф5400 H 8000mm 2存在问题 2.1 设备超负荷运行 随着煤气负荷的不断增加,因煤种频繁变化,进塔前H2S波动特别大,最高达4000 mg∕m3,有机硫最高达400 mg∕m3大大缩短了甲醇触煤使用寿命,下道工序工艺不达标,脱硫任务的完成也就成了泡影。内部再生能力明显吃力,对单质硫的析出,载氧体栲胶的氧化和V+5的转换带来很大难度,贫液混浊、再生不完全,且HS-和悬浮硫高,平均0.84g/L,付盐生成率高,析硫效果差,甚至堵塔现象十分频繁。 2.2 化工原材料消耗高 脱硫化工原材料消耗尽管和大多数同类型企业相比偏低,但是和理论数据相比还存在着较大的差距,每当入口硫化氢升高或系统出现波时,再生槽硫无法分离,大量的带清液硫泡沫,从溢流堰流至中间泡沫槽,造成溶液损耗高,给公司降本增效工作增添了较大的负担。 2.3 悬浮硫高 我们采用的湿法栲胶脱硫工艺,从总体上来看,工艺操作、工艺管理和各消耗都比较理想,从未因我们工序出现问题而影响系统生产,但悬浮硫较高一直是难以解决的问题,平均0.8g/L以上,硫堵塔现象十分频繁,每年大小修必须清塔,经过多次工艺调试,不能很好地控制在指标以内,后来我们加强了工艺操作溢流管理,也仍是如此。 从以上工艺流程图和设备规格情况可以分析出,设备偏小是造成该工艺出现问题主要因素,再加上煤炭市场紧缺,质量发生变化,在本来本工序设备超负荷运行的同时更是雪上加霜,脱硫循环量和再生成了工艺上的主要矛盾,加大循环量时,溶液在再生槽停留时间短,若减小脱硫循环量脱硫效率又很难保证。 3采取措施 见此现状,我们根据栲胶和“888”脱硫催化剂的特点进行了综合对比,讨论分析出“888”催化剂能提高脱硫效率、能脱除有机硫的和降低悬浮硫的特性,通过理论计算出投入量,而后利用循序渐进慢慢置换的办法,投入了该产品。 4投入后的效果 4.1 硫回收和悬浮硫的变化 在该产品初步投入一周后,再生槽硫泡沫层发生了变化,比重增加,质量得到了提高,硫回收率明显提高,降低了悬浮硫含量,在未投用“888”脱硫催化剂之前,贫液中总是有细小硫颗粒,拿不出来,在做分析时特别不好过滤,真空泵抽时需要40分钟,甚至需要更长时间,但随着“888”在溶液中慢慢置换,开始发挥出其作用,分析过滤时间明显缩短,仅需要五分钟就可以完成,分析结果也由原来的0.8g/L降低到0.3g/L以下,至今已数年一直比较稳定。随之看到的脱硫塔阻力在450mmH2O柱以下,一直比较稳定,填料已连续六年未进行清理和更换。为集团公司节约了大量的人力、物力和财力,确保了系统的长周期、高负荷稳定运行。 4.2 脱硫效率的变化 在本工序脱硫装置本来就超负荷运行同时,煤质的变化对脱硫的影响已是不容忽视的问题,入口硫上涨、焦油含量高而且气味较浓,溶液被污染,直接影响到再生系统正常工作,脱硫效率也慢慢得不到保障,为此,我们在内部大做文章,想方设法来提高溶液循环量,例如:在再生槽贫液区加连通管、取消泵入口过滤器等等…,尽管循环量得到了提高,但再生系统却背上了沉重的包袱。自投用“888”脱硫催化剂之后,这一矛盾得到了很好解决,循环量由原来的720m3/h降到600m3/h,脱硫效率仍然保持在99.7%以上,不但提高了溶液在再生槽的停留时间,而且解决了脱硫、再生的矛盾问题,实现了良性循环。 4.3 化工原材料消耗的变化 说起消耗,直观来说,它与硫化氢的含量有直接关系,我们制备的溶液是由纯碱、栲胶、五氧化二钒和“888”四种原料相匹配的混和液体,通过我们长期使用总结,“888”脱硫催化剂本身确实有脱硫和节约化工原材料的功效。当我们刚开始投用该产品时,也没有注意到这一点,只是让它起到卸硫的作用就行了,可是经过数月运行后,发现各化工原材料加入量逐渐减少后,工艺指标却丝毫未降,让我们迷惑不解,尤其是碱耗:在入口硫化氢平均1200mg/m3的时候,每天加碱200–300kg,仍能保持指标不下降,脱硫效率稳定,现平均0.52kg/tNH3,栲胶的加入量,也大量减少,原来每天平均加75kg,现只需加30kg,就完全能维持指标;五氧化二钒原来每月需加300kg,现每月只需加75kg,完全够用,而且副反应控制较好。自2004年以来,我们的吨氨耗化工原材料一直平均保持在2.8元左右,每年可为公司节约70万元以上,受到了各级领导的好评。 5近几年工艺运行数据: 1)、煤气流量:半水煤气60000Nm3∕h 水煤气36000 Nm3∕h 2)、原料气硫化氢:入口1200 mg∕m3 出口2 mg∕ m3以下 3)、脱硫效率:99.8% 4)、脱硫液循环量:合成氨:600 m3∕h 甲醇:380 m3∕h 5)、贫液组分:总碱度:24 g∕L Na2CO3:5 g∕L 栲胶1.0 g∕L 888脱硫剂15 PPm NaVO3:0.7 g∕L Na2S2O3:4 g∕L Na2SO4 : 20 g∕L NaCNS :35 g∕L PH值:8.6 6)、贫液中悬浮硫:0.3 g∕L以下 7)、硫回收率:78%以上 硫黄纯度:95%以上。 8)、化工原料消耗如下表: (kg∕tNH3) 原料 年度 纯碱 栲胶 五氧化二钒 888脱硫催化剂 备注 2006年 0.56 0.055 0.0045 0.0017 2007年 0.54 0.045 0.0042 0.0014 2008年 0.54 0.043 0.004 0.0014 6 管理和经验总结 6.1 人的管理 除了有一批熟练的脱硫工艺操作和分析工以外,最主要是得有一个对脱硫业务技术素质高和对本工艺极其认真负责的工艺管理人员,每天要坚持到工作岗位上通过分析数据检查工艺变化情况,尤其是对溶液组分的调节,每天加入化工原材料的量,必须做到了如指掌,力争做到精细化管理,严格禁止工艺指标和化工原料欠帐。 6.2 工艺调整 对于脱硫工艺调节是本工序最主要环节,它兼顾的面很广,关键是要找准其中的折中点,例如:有时发现溶液组分下降后,会大量补加化工原料,这时千万要注意三点:一是查找原因;二是补加方法;三是配新鲜液的质量把关,尤其是在工艺不稳定时更应该小心谨慎,如同人吃饭一样,一顿多一顿少,时间长了肯定会对身体健康产生坏的影响,调整工艺指标也是如此,一定要悠着性子慢慢调节,采取循序渐进的办法,做到少加勤加。特别是载氧体或催化剂的补加,必须考虑到它在系统的有效存活时间,由于它监测含量的手段是比色法,氧化态和还原态分析结果有一定的误差,可以说是一个隐形的指标,看分析结果很容易造成判断失误,这时工艺调节必须做到心中有数,若是盲目补加,不但浪费了化工原料,而且给脱硫液的及时恢复带来一定的难度。 6.3 再生槽溢流操作的管理 对于脱硫工艺来说,再生槽溢流也是脱硫工艺的关键环节,它能直接影响到贫液质量、吸收、塔阻、硫回收等等…乃至整个系统的生产,专设一操作工专门负责溢流,也是非常有必要的,是稳定悬浮硫指标的关键措施。再则,再生槽硫泡沫的变化是非常复杂多变的,例如:煤气质量、硫化氢的高低、残液的回收、再生吸气量、催化剂的指标控制等,都能使泡沫受到影响。所以我们要严格控制好硫泡沫的厚度和硫泡沫少的问题,一旦硫泡沫反应层增厚或没有硫泡沫,悬浮硫就会增长,必须做到根据硫泡沫情况,及时调节空气吸入量,或调节催化剂加入量。现在好多兄弟企业,使用的是连续熔硫,为了减少进入连续釜的泡沫液量,对再生槽溢流管理置之度外,我想,塔堵现象也是必然。 7副盐的生成和控制总结 1)脱硫工艺副盐生成是不可避免的,若控制不好,付反应生成,会导致碱耗大幅度升高,设备腐蚀加快。根据我们所掌握经验,副盐的生成途径很多,最基本的方式是要控制好溶液温度和溶液组分的浓度,两个指标的升高,都可导致副盐明显增高,对此我们应严格加强管理和控制,坚决把温度和溶液组分控制在最佳状态。其次健全分析项目是本工艺十分重要工作,尤其是对Na2S2O3、Na 2SO4 、NaCNS三个分析数据十分关注,几乎是每天都要进行分析,我们发现,付反应生成物的总和超过100 g∕L时,碱耗会大幅度升高,在我们公司就发生过两次类似事故,这是一个深刻的教训。 2)副盐Na2S2O3的控制,反应式中2NaHS+2O2=Na2S2O3+H2O控制的方法是加强再生,稳定最佳的溶液温度,在调整溶液循环量时兼顾到富液槽和再生槽的停留时间,提高NaVO3浓度是完全可以控制住的。我的经验是要降低该化合物,最好的办法是将其氧化成Na 2SO4,然后再降Na 2SO4效果较明显。从另外角度讲,尽管它是副盐生成物,此副盐在不高时,我发现它的存在却是有助于脱硫正常生产的主要指标,它能很好的反映出系统中HS-的转换正常与否,一旦该数据猛降,甚至降为2 g∕L以下时,再生槽的硫泡沫立即就会恶化,硫回收困难。 3)副盐Na2SO4控制,从反应式Na2S2O3+2O2=2Na2SO4+2S可以看出,通常来讲,它是由Na2S2O3过氧化生成的,根据我们的经验,一旦发现该数据增长,我们就补加NaVO3,控制其效果十分明显,例如:2009年2月23日我们分析发现该数据由19 g∕L ,缓慢上涨为25 g∕L,我们立刻在系统加了50Kg NaVO3,25日分析Na 2SO4发现降为14.4 g∕L ,下降了10 g∕L,从理论上来讲NaVO3、Na 2SO4是不发生化学反应的,有些技术人员认为是偶然的巧合,我认为不是如此,分析下降原因有两种1、补加NaVO3提高了硫化物的析出,随硫泡沫带走;2、“888”脱硫催化剂的作用。具体是什么原因我们还有待进一步探索研究确认。截止目前,我们脱硫液的硫代硫酸钠,一直控制在3g/L以下,最终产物硫酸钠控制在20 g∕L 左右,这两个数据控制已数年也一直比较稳定。 再则,残液的回收,也是导致副盐升高的主要原因,尤其是连续熔硫,硫回收后,溶液又回收至系统副盐却越积越多,应经过预处理后回系统最好。还有副盐硫氰酸钠是本工序较难控制的一生成物,只要控制脱硫液中总副盐是可以实现正常运转的,可暂时不管它的含量多高,目前唯一办法只有置换脱硫液了。 通过我们严格控制脱硫工艺中副盐,充分保证了化工原料的正常消耗,减少了对设备的腐蚀,提高了设备的使用寿命。稳定了生产。 总之,脱硫设备偏小,选择使用质量好的脱硫催化剂,加强脱硫工艺管理,合理调整工艺指标,认真总结和发现问题,使工艺得到及时调整,是完全可以使脱硫工序实现低成本良性循环的。
脱硫工艺良性循环总结
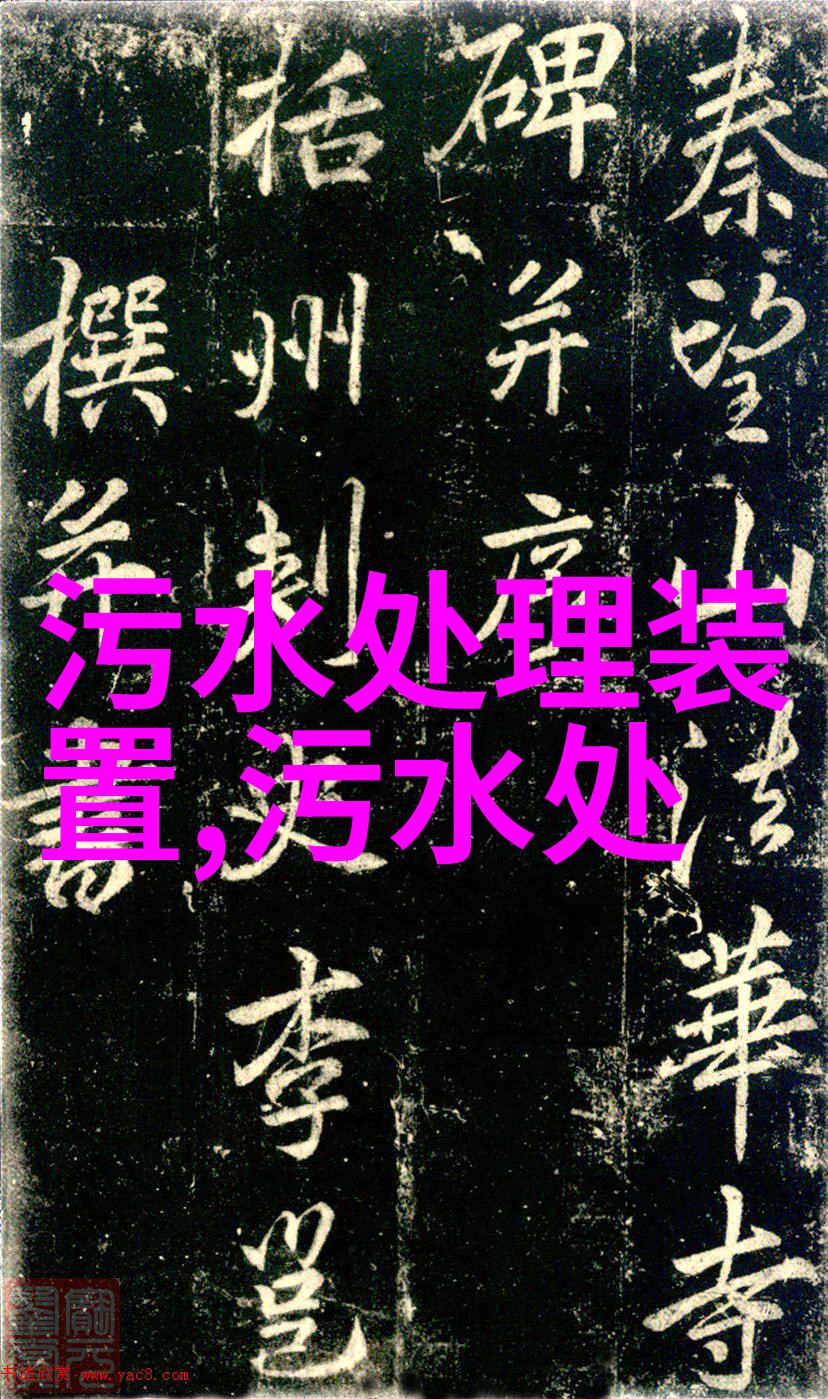